Just How Expert Packaging Machine Repair Provider Minimize Downtime and Boost Efficiency
Specialist packaging maker repair work solutions are vital in reducing downtime and boosting performance with specialized diagnostics and timely interventions. The implications of such solutions prolong past immediate repairs-- unloading the more comprehensive effect on operational effectiveness discloses important understandings right into long-lasting efficiency techniques - packaging machine repair service.
Value of Timely Repair Works
Prompt repair services of packaging equipments are crucial for preserving operational efficiency in any manufacturing atmosphere. When machinery breakdowns or breaks down, it can result in significant interruptions in assembly line, resulting in boosted downtime and lost earnings. The longer a product packaging maker stays out of order, the higher the influence on total efficiency, potentially creating delays in meeting orders and decreasing consumer fulfillment.
Along with the instant financial implications, delayed repairs can lead to much more comprehensive damage to the machinery. Elements that are not resolved immediately can deteriorate additionally, calling for even more pricey repair work or total replacements, which could have been stayed clear of through prompt intervention. Routine maintenance and prompt repairs can boost the lifespan of packaging devices, ensuring that they run at optimal performance levels.
Purchasing professional product packaging device repair work solutions is vital for alleviating these threats. A proactive strategy to repairs not just keeps manufacturing routines yet likewise promotes a culture of reliability within the organization. By prioritizing prompt repair work, services can maintain their one-upmanship, optimize resource appropriation, and ultimately enhance their profits with boosted functional performance.
Competence in Diagnostics
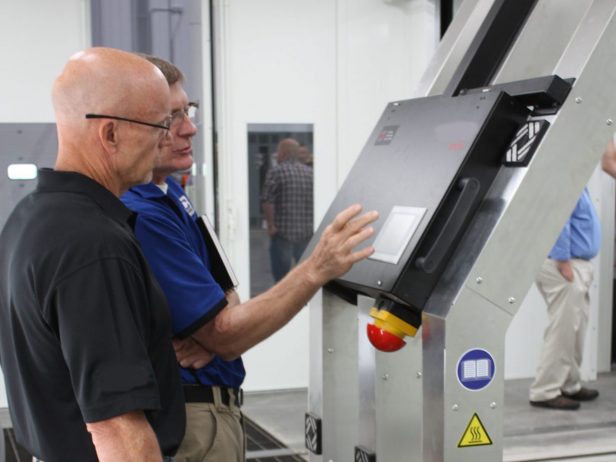
Reliable diagnostics not just facilitate swift recognition of troubles yet also improve the total integrity of product packaging procedures. By performing comprehensive assessments, technicians can examine the wellness of essential components, making certain that also small irregularities are attended to without delay. This interest to detail reduces the risk of unanticipated breakdowns, which can result in pricey downtime.
Additionally, specialist diagnostics supply useful insights into functional trends, permitting organizations to make informed decisions regarding tools upgrades or alterations. By leveraging these insights, companies can maximize their packaging procedures, bring about boosted efficiency and efficiency. Eventually, buying diagnostic expertise is crucial for organizations seeking to preserve seamless procedures and support high standards of top quality in their product packaging processes.
Preventive Upkeep Conveniences
Preventive upkeep matches specialist diagnostics by proactively resolving possible problems before they materialize right into severe issues. By carrying out a structured preventative upkeep program, business can considerably lower the danger of unexpected device failures, thus decreasing pricey downtime. Regular inspections, cleaning, and parts replacement assistance make sure that packaging equipment operates at ideal performance.
One of the vital advantages of precautionary upkeep is its capacity to prolong the lifespan of tools. By on a regular basis keeping equipment, businesses can avoid the worsening impacts of damage that typically cause major repair services or replacements. packaging machine repair service. This not only saves resources yet likewise improves the overall reliability of production processes
Furthermore, preventive upkeep adds to boosted security conditions within the workplace. By recognizing and rectifying possible risks before they intensify, organizations develop a safer environment for their employees. This positive technique not only safeguards employees yet additionally cultivates a society of duty and caution.
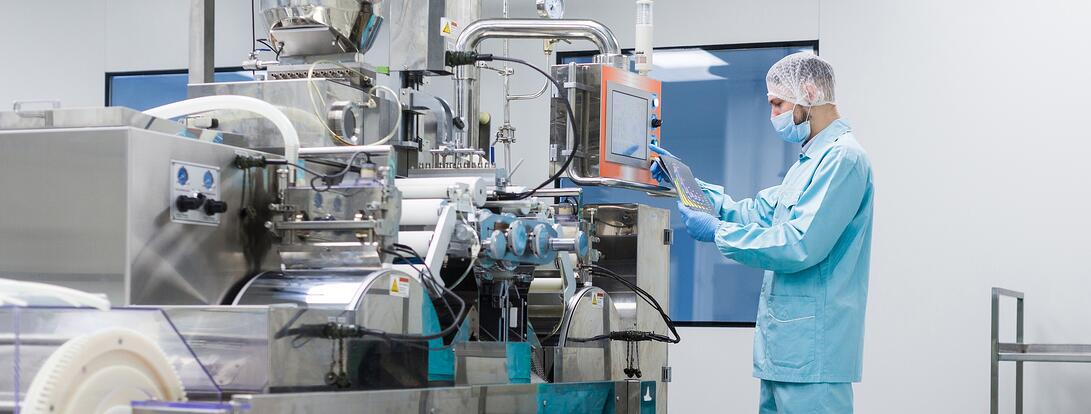
Personalized Service Solutions
Identifying the unique needs of each organization, customized service remedies for packaging maker repair work offer customized approaches that improve operational effectiveness. These services are designed to address specific obstacles dealt with by different markets, ensuring that device downtime is decreased and productivity is optimized.
Professional repair service services begin with a thorough evaluation of a company's product packaging operations. By understanding the particular equipment included and the demands of the production environment, professionals can develop a personalized repair and maintenance web plan. This may include specialized training for in-house team, the implementation of predictive upkeep innovations, or the arrangement of committed assistance throughout peak production times.
Additionally, tailored remedies can include adaptable solution agreements that line up with a firm's operational schedule, enabling repair services to be carried out during off-peak hours. By focusing on the special requirements of each organization, these bespoke options guarantee that fixings are not only reliable but also effortlessly incorporate into existing workflows.
Inevitably, the emphasis on modification allows firms to maximize their packaging processes, resulting in enhanced reliability and efficiency of equipment, which is important for keeping affordable benefit in today's fast-paced market.
Effect On General Effectiveness
Customized solution solutions not only address certain fixing requirements however additionally play a significant duty in boosting general operational performance. By providing targeted interventions, professional product packaging equipment fixing solutions straight decrease the frequency and period of equipment failures. This proactive method guarantees that assembly line continue to be operational, minimizing disturbances that can lead to expensive downtime.
Furthermore, effective repair service services add to smoother operations, as properly maintained machinery operates at ideal performance degrees. When devices function properly, the high quality of packaged products boosts, bring about fewer issues and less rework. This enhancement not just increases efficiency but also reinforces consumer fulfillment.
In enhancement, regular upkeep and quick action times from repair service specialists cultivate a culture of reliability within the company. Employees can focus on their primary jobs rather than bothering with potential devices break downs. The total throughput of the production procedure increases, enabling companies to meet demand extra properly.
Ultimately, the calculated investment in find more information expert repair work services translates to boosted efficiency across all operational aspects, making certain that businesses can adjust and prosper in an open market. This synergy in between maintenance and efficiency is vital for long-lasting success.
Final Thought
In verdict, expert product packaging maker repair service solutions play an essential function in reducing downtime and boosting efficiency within making atmospheres. Prompt fixings, expert diagnostics, and preventive upkeep add to the reliability of tools, while customized solution remedies resolve details functional needs. The collective effect of these services results in boosted general efficiency, enabling businesses to maintain manufacturing timetables, copyright learn this here now product quality, and efficiently satisfy market needs. Buying such solutions ultimately drives continual functional success.